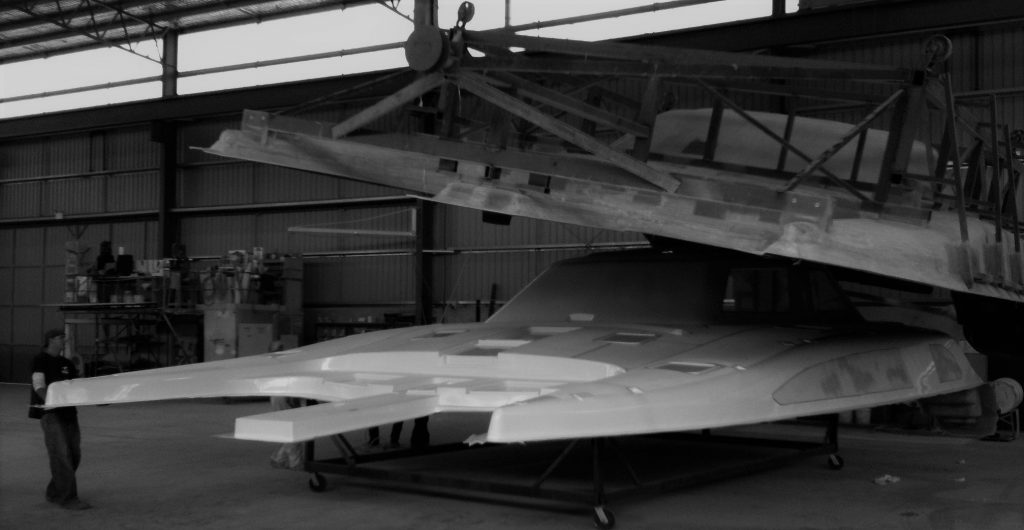
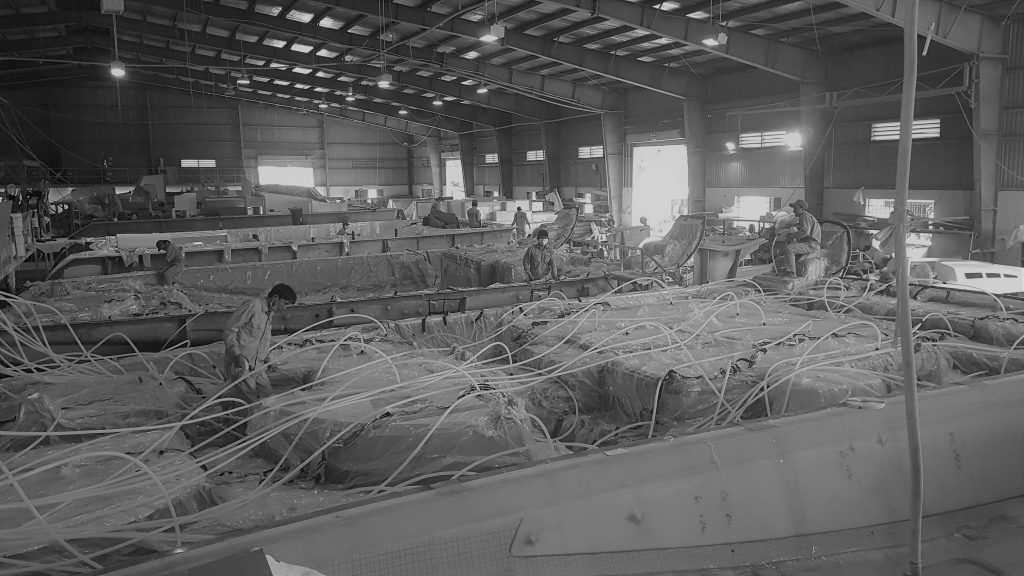
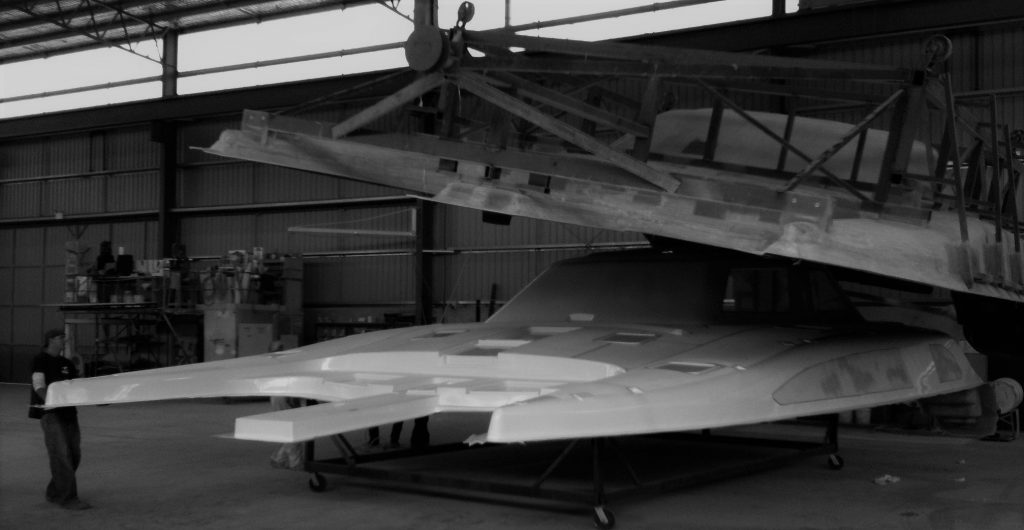
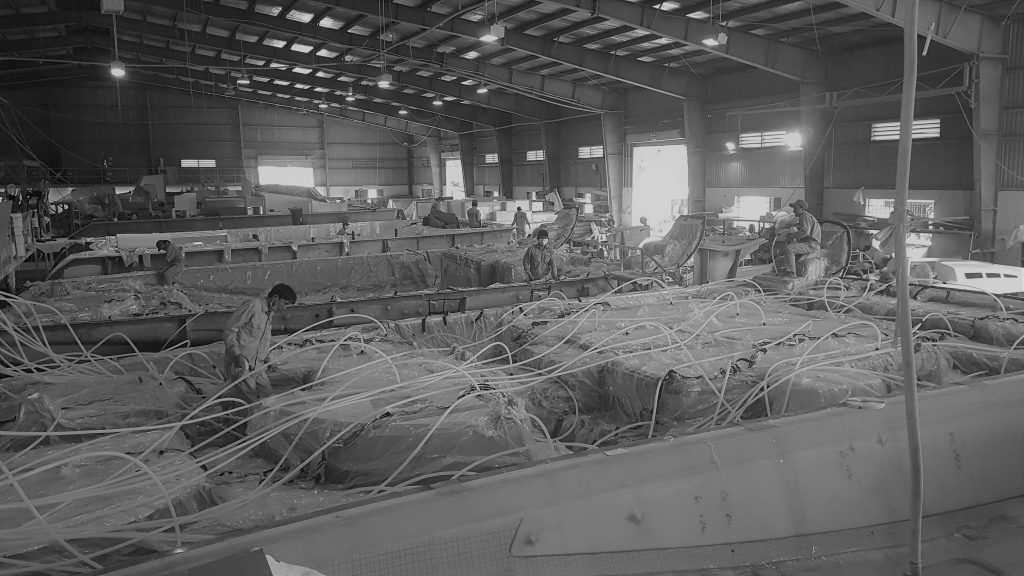
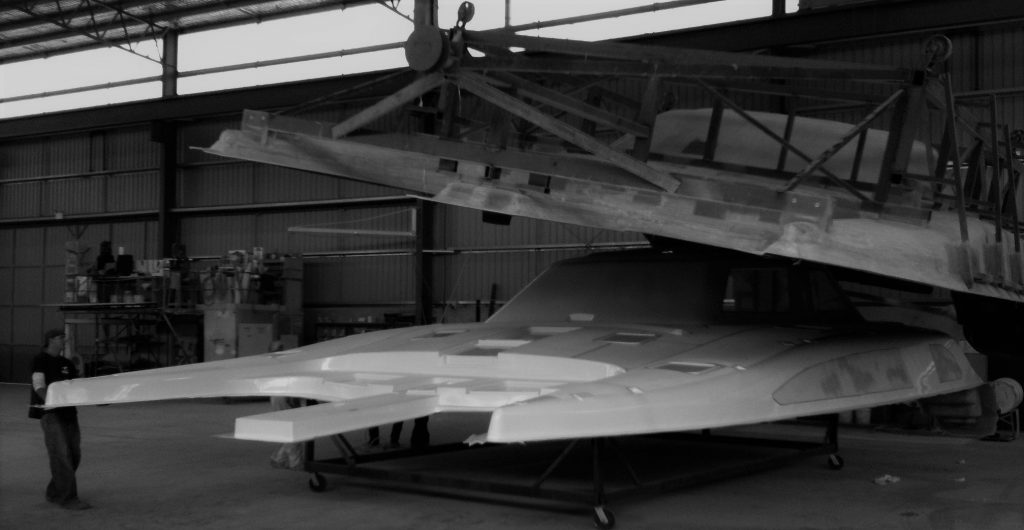
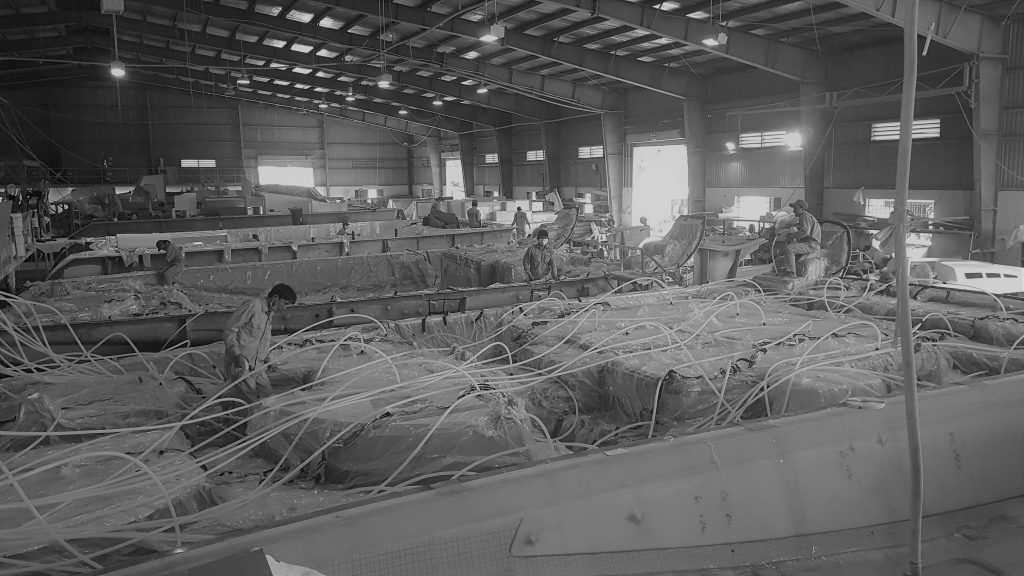
AU SOMMET DE L’ART DE LA CONSTRUCTION COMPOSITE
Seawind reste en continuel développement au fil des modèles, se construisant sur les connaissances et le succès des précédents modèles. Chaque voilier est le résultat collectif de milliers d’heures d’expérience en multicoque et des meilleures techniques de construction que le monde a à offrir.
AU SOMMET DE L’ART DE LA CONSTRUCTION COMPOSITE
INNOVATIONS EN INFUSION DE RÉSINE
Seuls les meilleurs matériaux sont utilisés dans la construction de nos navires. Qu’il s’agisse de dérives et de mâts en carbone, de fonds de coque en kevlar, de structures en fibre de verre ou d’âmes thermoformées, nous utilisons uniquement le nec plus ultra ! Nous achetons nos matériaux dans le monde entier, à la recherche constante de meilleure et nouvelles technologies. Nous ne le faisons pas pour construire les bateaux les plus rapides ni même les plus légers du monde, mais pour fournir à nos clients le meilleur rapport qualité-prix possible.
AU SOMMET DE L’ART DE LA CONSTRUCTION COMPOSITE
INNOVATIONS EN INFUSION DE RÉSINE
Les partenariats avec les leaders de l’ingénierie composite ont permis à Seawind de se concentrer sur l’optimisation des processus de fabrication tout en partageant la vaste expérience de production avec les équipes techniques d’experts en composites Diab, High Modulus et ATL.
AU SOMMET DE L’ART DE LA CONSTRUCTION COMPOSITE
INNOVATIONS EN INFUSION DE RÉSINE
Seawind a toujours été un leader technologique, à la fois en innovant dans les nouveaux outils mais également en adoptant de nouveaux procédés de fabrication. L’entreprise a utilisé des stratifiés formés sous vide tout au long de son histoire et s’est lancée dans la construction de coques par infusion en 2007. Depuis, nous avons parcouru un long chemin avec toutes nos pièces maintenant fabriquées à 100% sous vide. En effet, nous sommes fiers d’affirmer que nous ne possédons pas une seule machine à découper, un outil utilisé dans l’ensemble de l’industrie pour produire rapidement du composite bon marché au détriment du poids et de la résistance.
AU SOMMET DE L’ART DE LA CONSTRUCTION COMPOSITE
INNOVATIONS EN INFUSION DE RÉSINE
Seawind emploie la technologie de l’infusion de résine afin de produire un bateau léger, solide et plus respectueux de l’environnement. En partenariat avec High Modulus et DIAB Technologie, le procédé complexe d’infusion a été développé en utilisant un modèle de simulation numérique 3D (illustré ci-dessous) afin d’assurer que la meilleure qualité et uniformité soit atteintes dans chaque nouveau Seawind.
AU SOMMET DE L’ART DE LA CONSTRUCTION COMPOSITE
INNOVATIONS EN INFUSION DE RÉSINE
Seuls les meilleurs matériaux sont utilisés dans la construction de nos navires. Qu’il s’agisse de dérives et de mâts en carbone, de fonds de coque en kevlar, de structures en fibre de verre ou d’âmes thermoformées, nous utilisons uniquement le nec plus ultra ! Nous achetons nos matériaux dans le monde entier, à la recherche constante de meilleure et nouvelles technologies. Nous ne le faisons pas pour construire les bateaux les plus rapides ni même les plus légers du monde, mais pour fournir à nos clients le meilleur rapport qualité-prix possible.
AU SOMMET DE L’ART DE LA CONSTRUCTION COMPOSITE
INNOVATIONS EN INFUSION DE RÉSINE
Les partenariats avec les leaders de l’ingénierie composite ont permis à Seawind de se concentrer sur l’optimisation des processus de fabrication tout en partageant la vaste expérience de production avec les équipes techniques d’experts en composites Diab, High Modulus et ATL.
AU SOMMET DE L’ART DE LA CONSTRUCTION COMPOSITE
INNOVATIONS EN INFUSION DE RÉSINE
Seawind a toujours été un leader technologique, à la fois en innovant dans les nouveaux outils mais également en adoptant de nouveaux procédés de fabrication. L’entreprise a utilisé des stratifiés formés sous vide tout au long de son histoire et s’est lancée dans la construction de coques par infusion en 2007. Depuis, nous avons parcouru un long chemin avec toutes nos pièces maintenant fabriquées à 100% sous vide. En effet, nous sommes fiers d’affirmer que nous ne possédons pas une seule machine à découper, un outil utilisé dans l’ensemble de l’industrie pour produire rapidement du composite bon marché au détriment du poids et de la résistance.
AU SOMMET DE L’ART DE LA CONSTRUCTION COMPOSITE
INNOVATIONS EN INFUSION DE RÉSINE
Seawind emploie la technologie de l’infusion de résine afin de produire un bateau léger, solide et plus respectueux de l’environnement. En partenariat avec High Modulus et DIAB Technologie, le procédé complexe d’infusion a été développé en utilisant un modèle de simulation numérique 3D (illustré ci-dessous) afin d’assurer que la meilleure qualité et uniformité soit atteintes dans chaque nouveau Seawind.
Après l’acquisition par Seawind de Corsair Marine International en 2010, l’une des premières étapes de la transition a été d’identifier les points forts des deux sociétés, en s’assurant à ce qu’aucune de leur forces respectives ne soit perdue lors de l’intégration de la production des catamarans Seawind. Seawind avait de nombreux atouts à offrir en tant que constructeur renommé de catamaran de croisière fiable. Corsair a su montrer une innovation remarquable en termes de méthode de construction et de stratification, en témoigne les performances exceptionnelles de ces trimarans. Néanmoins, leurs innovations se sont plus focalisées sur la recherche de gain de poids que ce qui était nécessaire à la gamme de voilier Seawind plus orienté vers la croisière.

L’influence la plus notable de l’acquisition de Corsair Marine sur les catamarans Seawind fut le gain de poids dans les techniques composites. Comme la plupart des constructeurs de catamarans, Seawind utilisait du mat de verre en guise de peau de coque et de structure. Le mat était projeté à l’aide d’un pistolet coupant les fibres de verre en bout de 40mm et les mélangeant à de la résine et du catalyseur dans le même temps. Cette méthode du “mat projeté” permettait d’appliquer de la matière rapidement mais en étant restreint à utiliser du mat, en opposition aux tissus beaucoup plus structurels tel que le biaxial, quadri-axial ou unidirectionnels mais devant être appliquer à la main.Pendant longtemps cette méthode du mat projeté fut la technique la plus utilisée au monde dans la construction navale composite. C’était la méthode requérant le moins de main-d’œuvre possible comparée à toutes les autres méthodes d’application disponibles. Comme ces brins de fibres n’étaient que très petits et ne chevauchaient que très peu, l’application devait être épaisse en appliquant plusieurs couches pour obtenir une résistance similaire à celle d’un tissu. Le rapport résine fibre n’était que de 2:1 au mieux (2 volumes de résine pour 1 de verre).
Les techniques actuellement utilisées sur les voiliers Seawind impliquent de positionner manuellement les tissus (cette méthode était auparavant trop coûteuse). Ces tissus comprennent des fibres orientées multi directionnellement couvrant toute la largeur du rouleau.
En plus d’une utilisation plus intelligente des matériaux, nous consolidons également tous les composants (par le processus de saturation du verre en extrayant la résine en excès) des coques, du pont, petites garnitures et trappes d’accès, à l’aide du processus du sous vide ou de l’infusion. Ces procédés produisent non seulement une structure beaucoup plus solide, mais permettent de sortir des pièces à une fraction du poids et avec un rapport résine/fibre optimal de 1:1, 30% plus léger a piece égale (avec le même volume de fibres).

Nous avons également investi en recherche de matériaux alternatifs y compris pour les âmes des sandwichs. Pour les pièces les plus volumineuses les matériaux n’ont pas été changés, cependant ceux qui qui l’ont été ont donné des résultats remarquables. Le contreplaqué précédemment utilisé dans les zones boulonnées du pont a maintenant été remplacé par de la mousse PVC haute densité à cellules fermées. Toutes les equipés,les séparateurs et les cloisons précédemment construits en contreplaqué marin sont maintenant des panneaux en fibre de verre sandwich en mousse PVC. La construction sous vide donne une plus grande résistance, un poids inférieur tout en éliminant les risques de moisissure ou de décomposition. Une partie de cette technologie a également profité à d’autres départements tels que l’assemblage bois, tables, portes et étagères étant construits en sandwich plutôt qu’en panneaux de bois lourds et massifs.

Les principaux avantages d’un bateau léger nous ont toujours été évidents. Un voilier plus léger montrera de meilleures performances, à la fois au moteur ou sous voile. L’économie de carburant est notable et de ce fait, les destinations sont atteintes plus rapidement. De plus, notre chasse aux kilos a clairement bénéficié à de nombreux autres domaines. Les matériaux et les processus utilisés afin de réduire les poids ont abouti à une structure plus solide. Par conséquent, et par un cercle vertueux qui s’installe, le poids éliminé permet de réduire le stress sur la structure globale. Les matériaux et équipements que nous installons actuellement sont d’un niveau supérieur à ceux utilisés auparavant. Non seulement les catamarans en deviennent plus rapides, mais ils sont également plus faciles à manœuvrer que tout ce que nous pouvions imaginer.
Page
LANGUE
NOUS CONTACTER
© 2025 Seawind Group Holdings, Pty Ltd. All rights reserved.